Web Tension Control for Web Handling
October 5, 2021
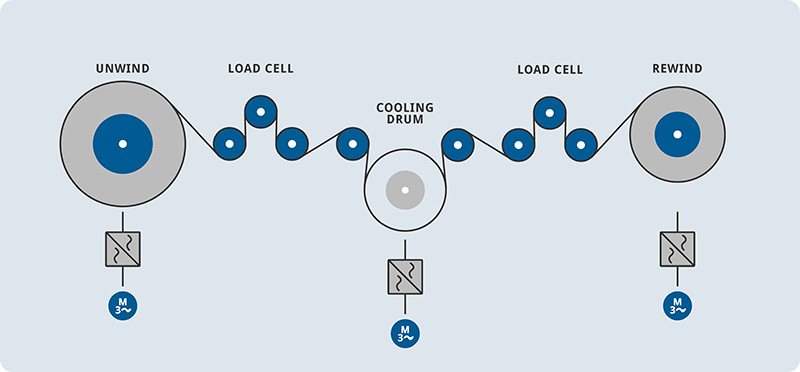
Web Tension Control For Web Handling Basics
In coordinated drive systems on production machines, coordination is the operation of all individual sections and the overall control so that the process machine functions as a single entity.
This means that all drives and devices (sections) must stop and start together, accelerate and decelerate together, and compensate for process variations similarly and smoothly. Production machines need to transfer the web (or substrate being produced and processed) from one end of the machine to the other.
To control a coordinated system, a web tension control system is often needed for the task. There are two types of tension control:
- Direct: measures tension of the web directly as the web transfers over a designated tension roll.
- Indirect: measures or calculates tension indirectly by using either the position of the web in relation to a fixed roll or open-loop torque controls.
Why is Web Tension Control Critical?
Proper tension control allows consistency and high quality for the web or substrate being processed. Whether it’s a building product, steel or aluminum, or converting processes, tension control affects the thickness, coating weight, density, wrinkle mitigation, or wound roll quality of the final product. Typical applications in web handling that need proper web tension control are winders and unwinders, coaters, laminators, accumulators, and pull rolls. Minimal product defects are mitigated by good quality tension control.
Improved Product Quality
There are a number of problems that can arise due to improper tensioning during the winding process. For winders, common defects include wrinkles, starring or telescoped wound rolls, and crushed cores. The web can also suffer stretching with the extensible web when processing film. Sheet breaks can occur from improper coordination combined with non-compliant tension control, causing unwanted production machine downtime.
Faster Setup, higher operator efficiency
An optimized web tension control system allows operators to quickly and consistently recreate the proper tension of any web. This will sometimes allow a single machine to run different products or material types with different settings and under a variety of conditions, allowing for quick changeover of products.
Higher Productivity
Optimized tension control allows production machines to be run at the highest design speed with some overspeed capabilities, only limited by the process and the mechanics. If the tension control is robust, it can run or ride through abnormal material or substrate, as with being able to control through unexpected mechanical deviations.
Proper tension control can keep production machine utilization high, all while producing more product. Plus, optimized tension control will eliminate many web breaks because of non-compliant material and mechanics, as well as operator errors, thus reducing waste and lost production time.
Multiple Tension Zones
Multiple tension zones are common on almost all production machines. Again, production machines need to transfer the web (or substrate being produced and processed) from one end of the machine to the other. Typically, these lines consist of:
- From an extruded feed, casting feed, or an unwound roll (unwind zone),
- Process section zones,
- Exit cut to length or exit rewind zones.
For each zone to work correctly and in conjunction with the other sections, a coordinated control system must be implemented. Sectional controls are developed to control each zone. Each section may be called a tension zone. Properly isolating sections is also critical for each section’s ability to absorb variations in tension from section to section.
There are many methods for creating a tension isolation section. Sometimes, a driven steel pull roller with a pivoting rubber-covered nip roll will be used. Or, an s-wrap or bridle-driven roll section can also be successful, as long as the roll surface’s frictional qualities are considered to ensure proper isolation and avoid slipping. They are usually designed to be able to handle a certain differential tension before slippage occurs. One example of no-contact nips is vacuum rolls.
Open-loop tension zones can be used mainly for the beginning and end of the line or when a torque control is needed (i.e., load share).
Tension Control for Unwind and Rewind Applications
In the unwinder and rewinder zones, not only does tension control need to be consistent, but there are many dynamics that need to be accounted for. As the roll builds up (winding) or down (unwinding), the roll diameter is constantly changing, and consequently, so is the weight of the roll. The shaft speed RPM also changes with the diameter (bigger diameter, lower shaft speed RPM), while the outside diameter web speed must remain constant. There are many things to account for besides the tension feedback device, including:
- Surface speed versus shaft speed
- Changing mechanics due to the weight of the roll, typically called “mechanical loss compensation” (i.e., variable inertia)
- Diameter sensing or calculation.
For a rewind, the surface tension sometimes needs a tapering tension function based on diameter: a reduction in the winder tension using a linear, hyperbolic, or custom function must be derived to prevent winding defects such as crushed cores, starring, or telescoping.
There are several types of winding mechanical configurations:
- Axial winder driven with a drive shaft,
- Axial winder with a slip core control,
- Surface winders,
- Center surface winders.
Open-Loop
Open-loop tension control systems are more complicated to set up due to the lack of a feedback device and the need to be more exact on your mechanical loss compensations as there is no feedback device for tension. The hardware is less expensive to install, but more costly to implement.
This type of system uses an indirect method for calculating or setting the section’s tension. It uses a torque regulation and must take into account the diameter of the roll, gearbox, and the inertia and friction to maintain constant tension.
An open-loop system is considerably more effective than a manual process, but it is not as accurate as an actual tension device. It is not recommended to use an open-loop system or open-loop torque for products or processes that require a very precise tension control.
Closed-Loop
A closed-loop tension control system uses a feedback device to measure the tension or position of a tension roller. One example is a load cell feedback, or it can be a strain gauge, or it can be a dancer position (measuring roller) to extract feedback for the “outer tension loop” controller. A force-measuring roller (also called a loadcell tension roller) is a common measurement device as it can measure the actual tension applied to the web and compare that with the setpoint.
In any case, whether it’s a tension device or a dancer roller with position, the outer loop trims the line speed setpoint or can be configured as trimming the tension/torque setpoint to achieve good tension control depending on the mechanical configuration.
A well-optimized closed-loop system can operate within two percent or less during steady-state and five percent or less during ramping of the machine of the tension setpoint, making it an ideal solution for a variety of products and processes. This, of course, depends on the mechanical compliance of the machine and web substrate.
Better Control; Better Results
Operating machines at high speeds while still achieving production quality is the key. Achieving this goal with web materials relies on maintaining proper tension from the unwinder or input material to the process section, then on to rewind or cut to length device, all while other variables are in play. Automated tension control processes allow for higher computational speeds as changes in tension are continuously monitored and adjusted automatically.
Choosing the right tension control system means a deep understanding of the web material, your automation needs, and the requirements of your existing machines, and then choosing an engineering team with the right experience working with a variety of sectional, control-based coordinated drive system applications.